
Usu Kuchi heavy
Fibre Content:100% Thai kozo
Fibre:Kozo
Usage:Printmaking, Silkscreen, Serigraph, Lithography, Relief Print, Linocut, Woodcut, Collograph, Intaglio, Etching, Water Based, Oil Based, Brush Painting, Stencil, Collage, Orizome, Suminagashi, Bookbinding
Weight:31g
Size Imperial:25 x 37"
Een zeer goede kwaliteit machine made papier. Goed absorberend en neemt kleur goed op
An excellent quality machine-made paper. Very cloth-like when Konnyaku is applied. Absorbent, takes colour well. Also available in Extra Heavy (65g)
About Kozo
Kozo is used as a general term for Japanese paper made from the inner bark of mulberry trees, such as the Mulberry paper Broussonetia papyrifera and bast paper fibers harvested from that plant.
The UNESCO-designated papers are all made using the same painstaking
process that artisans have been using for centuries. It begins by
steaming the kozo until the the bark becomes soft enough to be stripped
away. The inner bark is rinsed—traditionally in the cold flow of a river
or stream, which also exposes it to sunlight that naturally bleaches
it.
The bleached bark is boiled in an alkaline soda-ash solution
to remove the pectin that binds the bark fibers together. Then,
papermakers embark on a painstaking process called chiritori, where the fibers are placed in frigid water, while the papermaker carefully plucks out lingering specks of dirt and dust.
From
there, the makers soften the fibers by beating them, and then mix them
in a vat with water and neri to form a pulp. A hinged wooden frame
called a suketa is dipped into the pulp to form sheets. The frame
closes to hold a bamboo mat, onto which the pulp fibers cross from a
gentle rocking motion. Finally, the sheet is removed from the frame,
pressed overnight, and placed on boards to dry. In all, it can take up
to several weeks for a batch to go from pulp to paper.
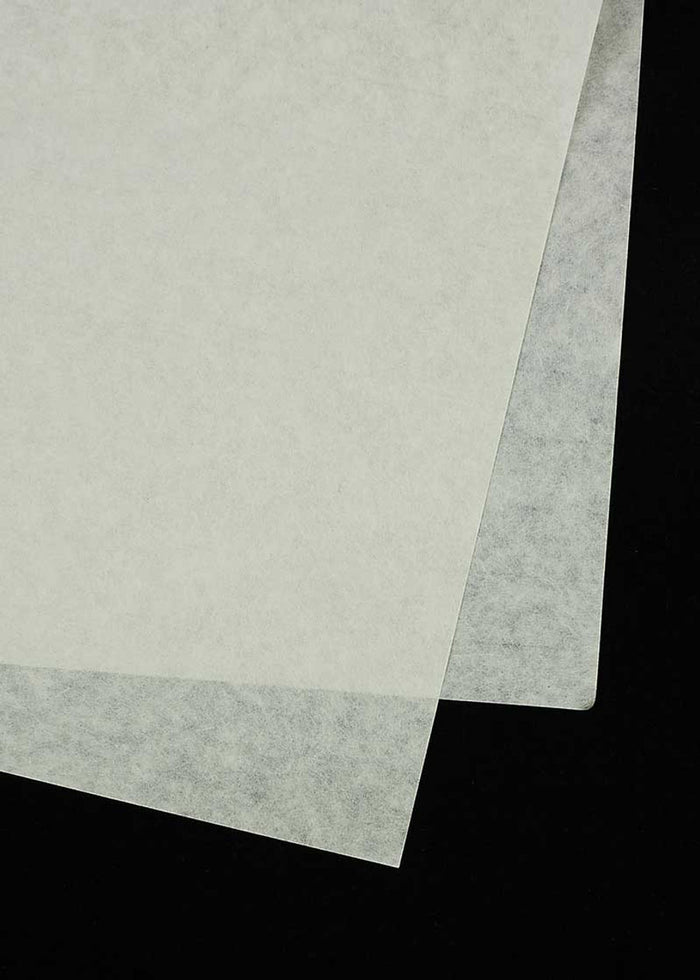
